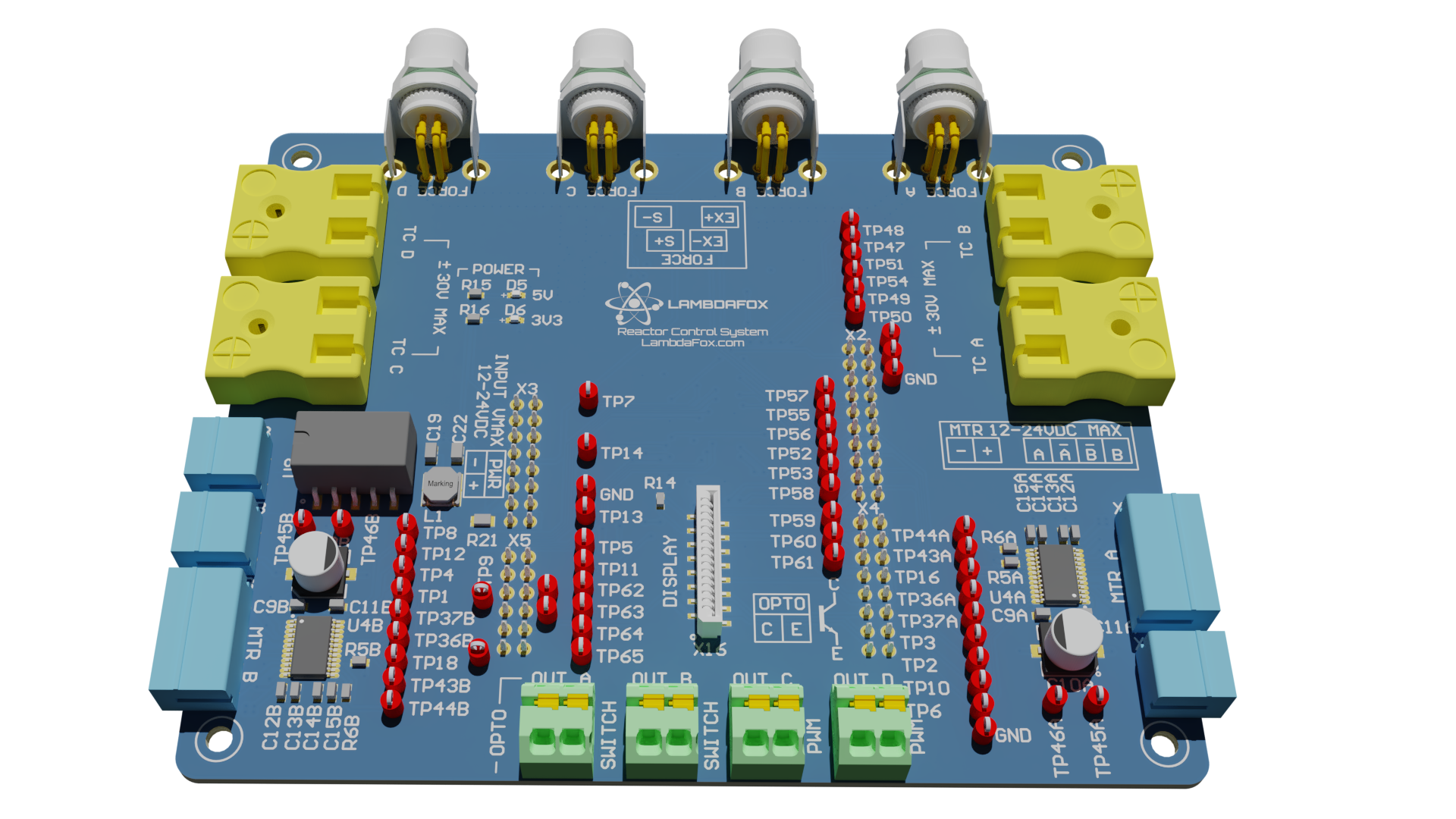
Overview
In this article we discuss the reactor control system design and features.
Table of Contents
Background
The reactor control system (RCS) is a fully automated control system targeted at the micro-reactors market for development and research of catalytic materials. It provides a low-cost entry for automation of pilot scale and laboratory research and development systems while offering extensive data logging capability and critical safety features including sequenced shutdown protocols as well as configurable warning, fault, and critical limits.
Features
Feature | Description |
---|---|
4 Channel Thermocouple Input | 0.01°C resolution supporting type K, J, and T thermocouples with connector reconfiguration |
Isolated Process Output | 4 isolated ouputs, 2 ON/OFF and 2 PWM capable outputs |
Logging | Support for logging to on-board micro-SD card |
Ethernet | On-board ethernet controller |
Pump Driver | Supports two peristaltic pumps or stepper drivers with independent power input |
4 Channel Bridge Amplifier | Low-noise 24-bit bridge/load cell amplifier with shielded M8 connectors |
Wide Input Voltage | Capble of being run from USB, or external 12-24VDC input for data logging or field applications |
Safe shutdown | Capable of monitoring all sensors concurrently against set safety and shutdown thresholds. If a fault is detected the system is capable of sequentially shutting down to prevent damage to components |
Hardware
Microntroller
Specification | Value |
---|---|
Part Number | MK64FN1M0VLL12 |
MCU Core | ARM M4 |
Clock Speed | 120 MHz |
Memory | 1 MB |
RAM | 256 KB |
The microcontroller used is an NXP MK64FN1M0VLL12. It is a competitively priced yet powerful 120-MHz ARM M4 microcontroller. It is extensively documented, has an excellent software API, and direct support from NXP representatives when needed.
Thermocouple Amplifiers
The thermocouple amplifiers are monolithic devices which offer a 0.01°C resolution and have proven to be repeatable and reliable even in industrial environments with electrical noise. They are calibrated after assembly to ensure absolute accuracy. Special care was taken to ensure no thermal gradients exist between the amplifier and the connector.
Load Cell Interface
The load cell interface consists of a 24-bit ADC with a multiplexed input. Using noise mitigation techniques we achieve more than 17 noise free bits with a 20.08 ENOB figure. This gives us an approximate resolution of 232mg for a standard 1mV/V 5kg load cell which is significantly better than the target of 500mg and allows for metering of fluids with varying densities. Additional methods can be used to increase the resolution if needed.
Shift Registers
The microcontroller had insufficient GPIO to support all of the needed pins and therefore a GPIO expander was implemented to provide an additional 24 outputs. The shift register was reserved for the configuration pins of the various devices to limit impact to high speed busses. The update rate of the expander has proven itself to be incredibly fast and un-noticable even in the most demanding of application logic.
Motor Driver
The system supports two stepper motors with a feature-rich acceleration capable driver. Each driver supports an independent power supply and motor connection using quick connect terminal blocks. The design was intended to be used with stepper-driven peristaltic pumps, however, is capable of operating with most NEMA17 or smaller stepper motors for customized user applications.
Isolated Outputs
The outputs are designed with isolation in mind. The isolator is rated for 3000V, however, the intended operation is designed for 24VDC industrial outputs therefore the creepage and distance between the connectors and adjacent devices governs the limit. The connectors are designed to be used with quick-wire ferrules and have a very solid positive locking mechanism similar to WAGO style terminal blocks.
Display Interface
The RCS supports a remotely mounted LCD display with encoder control. The interface to this display is a COTS flat-flex connector. If the display is not used it may be used as a GPIO expansion port.
Software Architecture
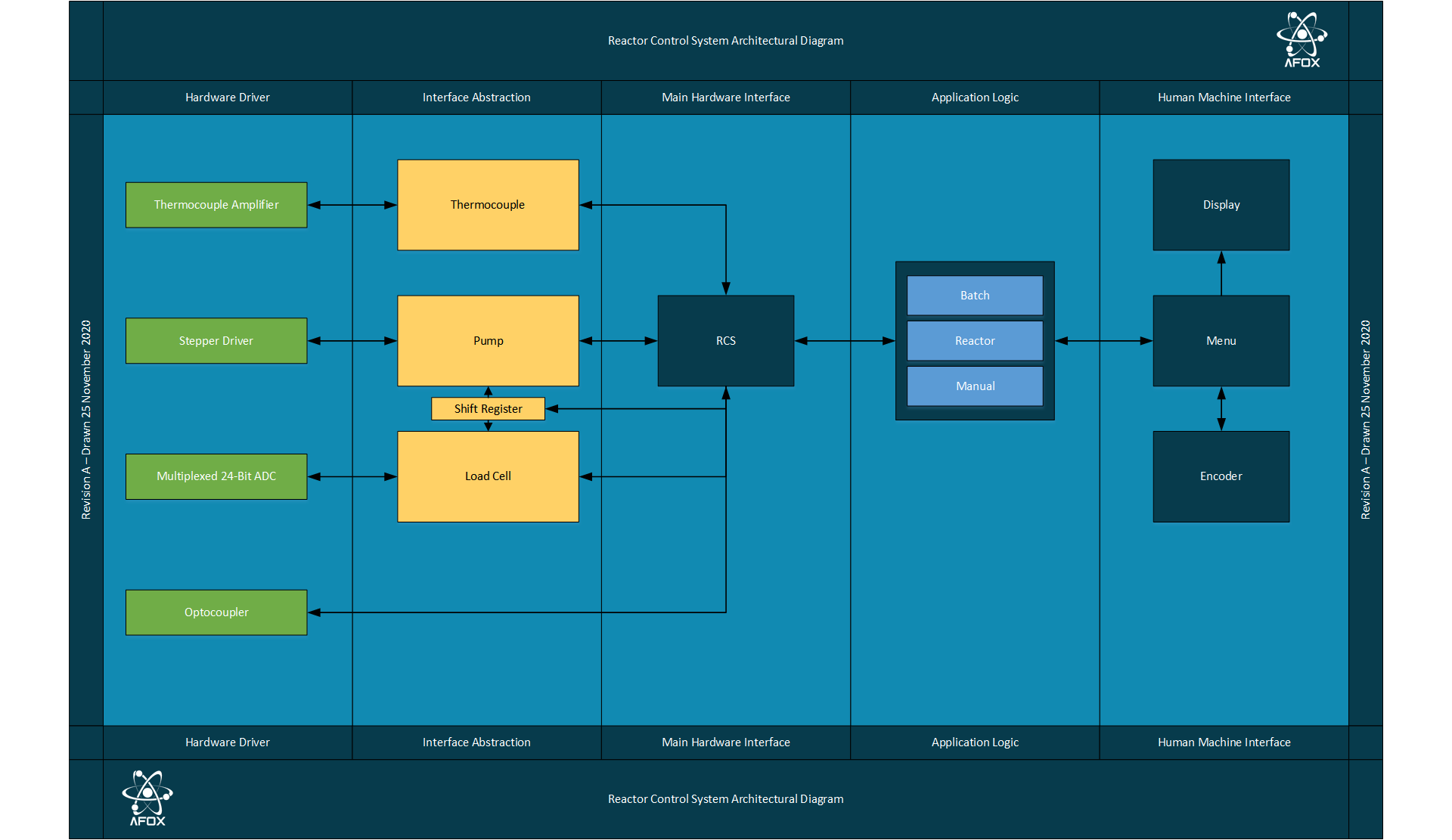
The reactor control system was architected in a layered manner to ensure safety and reliability. The core layer RCS allows a single application logic interface to the system hardware. This approach allows us to easily intercept all commands, and sensor data to monitor for potentially unsafe or damaging conditions.
Hardware Layer
The hardware drivers provide the interface to the base hardware. These would include specific commands to access registers, or functionality within the devices.
Interface Abstraction
The hardware interface abstraction layer provides the initialization of the base hardware. It handles multiple channels, GPIO access, and provides a single instance to talk to the base hardware through for the main application interface RCS
.
Each interface has unique features that allow for calibration data to be set, or interface to control algorithm logic for expanded functionality. The pump driver for instance features speed control logic to accelerate and decelerate the pump with proven pumping accuracy to greater than 0.1mL repeatably.
Main Hardware Interface
The main interface to the system for application logic is RCS or Reactor Control System. It abstracts away all of the lower functions such that the application logic only needs to talk to the RCS layer. Within the RCS layer we have monitoring and logging tasks which allow the system to monitor for faults, and log data for later analysis at configurable update rates.
Application Logic
The logic layer serves as the base functionality for the system. All modes and operation are controlled in this layer. This layer gets sensor data directly from RCS and will update the HMI (Human Machine Interfaces)
Documentation
All code has been extensively documented using the doxygen automatic document generation tool.
Final Notes
The RCS is a very powerful and cost effective tool. It has proven itself to be reliable and safe through extensive testing and field use. It continues to help researchers increase their productivity by allowing multiple experiments to be run simultaneously with a control operator capable of monitoring the systems remotely. Its data collection capabilities have replaced many thousands of dollars in data aquisition hardware while allowing for full traceability of measurements against time and calibration data in a very small footprint suitable for high density experiments.